On this Page
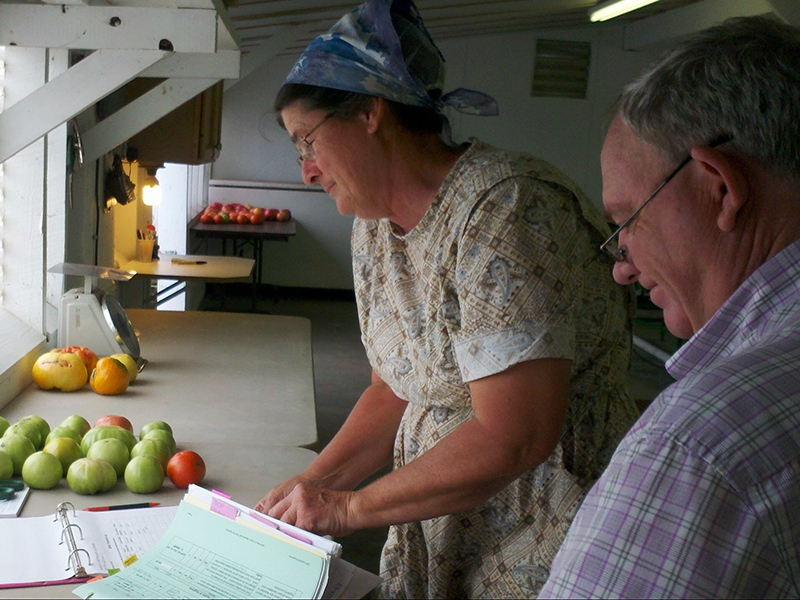
Frequently Asked Questions
Click on the questions below to see answers.
Does My Farm Need GAP Certification?
A common question we are often asked is, “Does my farm need to be GAP-certified?” To answer this question, it is important to consider market access. While a food safety audit is an absolute necessity with some larger retailers or wholesalers in order to sell product to them, other buyers, like restaurants, public schools, and direct sales venues like roadside stands and farmers market, typically do not require a food safety audit. Since requirements can vary within market sectors, talking with your prospective buyers first and asking them what they need in the way of food safety training, documentation, audits, and liability insurance, will provide direction and can save you a lot of unnecessary time, energy, and money.
You may use the “VCE Producer GAP Certification Inquiry Form” to look at your market(s) and explore what they require in the way of food safety practices, training, documentation, and verification. You can then send the form to the Fresh Produce Food Safety Team and/or your local VCE agent. Once received, VCE will review the form and discuss next steps with you about whether or not your farm needs GAP certification.
Audit Preparation Process Steps
Once you determine that you need to become GAP certified — based on your markets — there are a series of preparation steps to follow:
Assessing On-Farm Risks
The first step for preparing for your audit is to assess the on-farm risks as outlined in the Assessing On-Farm Produce Safety Risks section. While the factsheet series has comprehensive checklists to consider on-farm risks, you may wish to use a simpler questionnaire as you get started.
Manual Preparation
The next main step is to prepare your food safety plan or manual. Virginia Cooperative Extension has created manual templates for the USDA GAP, HGAP, and HGAP+ audits. The templates include the core elements needed for a food safety plan and provide an excellent starting point as you pursue certification. Given the complexity of the audit preparation process, we encourage you to work closely with the VCE FPFST or your local agent, so they can mentor you. The templates are available on Google Drive. Please contact Amber Vallotton at avallott@vt.edu , Ashley Edwards at aledwards@vt.edu, or Joanne Jones at jojenki1@vt.edu for more information.
On-Farm Implementation
As you are developing your food safety plan, it is important that you implement food safety practices in your operation and document that they are being performed. This means making any on-the-ground changes to infrastructure and product flow, as well as incorporating specific practices into the daily activities. It also means completing records at the appropriate times, following all cleaning and sanitizing procedures at their scheduled intervals, conducting water sampling and recording the results, as well as documenting any corrective actions that need to be taken.
Pre-Audit Walkthrough
To make sure you have addressed all the audit questions and have practices in place prior to your audit, it is helpful to conduct a pre-audit walkthrough or “mock audit” with your VCE Extension agent. The checklist at the end of the Assessing On-Farm Produce Safety Risks: Preparing for GAP Certification factsheet (FST-406NP) has been developed to help you with your walkthrough and follows the various questions contained in the audit checklists.
Walk through your fields or greenhouses and ensure the questions are addressed in all production, packing, and post-harvest handling areas. Make sure your logs and other records are easily accessible and filled out.
- Are workers following the food safety protocols they learned in training?
- Are your animal mitigation measures working?
- Do you notice any issues with your water system?
- Does your tested water satisfy appropriate microbial quality standards, and if not, are your water treatment measures correcting issues (verified by re-testing)?
- How clean is your packing shed and/or packing facility?
- Have you conducted a mock recall to test the effectiveness of your traceability program?
- Do you have all required documentation needed to support your activities?
- Is signage posted where needed?
- Overall, is the farm ready for an inspection? If there are any last-minute items to address, do so before the scheduled audit date.
Submitting Paperwork and Scheduling the Audit
Concurrent with working on your food safety plan manual and on-farm implementation, you will need to complete and submit the SC-430 Vendor Form to USDA/Agricultural Marketing Service. This will establish a billing account with USDA/AMS. If you already have an account but something has changed, you will need to re-submit the SC-430 Vendor Form with the updates.
Once your manual is nearing completion, all standard operating procedures are written and being followed, and applicable records are being kept, you should request an official audit. In Virginia, USDA audits are administered through the Virginia Department of Agriculture and Consumer Services Division of Commodity Services. VDACS inspectors act on behalf of the USDA to perform the official audit as an independent third party.
As a part of the official request for the audit, you will need to complete and send them Form SC-237A (USDA Agricultural Marketing Service Request for Audit Services Form) and the Agreement for Participation in Audit Services Form SC-651. The VDACS office will contact you and confirm the receipt of your request, give you more information about the program procedures, and schedule your audit.
Audit and Post-Audit Follow-Up
The day of the scheduled audit, the VDACS inspector will conduct an on-site inspection, in which they will review your food safety plan, supporting documents, and on-farm compliance. As they go through the audit, be prepared to answer any questions needing clarification. Once they conduct the site visit, they will send the completed paperwork to USDA AMS to review and finalize the certification. Once finalized, USDA puts the farm on their USDA AMS website, which lists all farms in the U.S. that have successfully passed their USDA GAP and HGAP audits. The listing is searchable by state and by commodity, thus providing a service to those farms certified. Keep in mind there can be a lag time between the audit date and this information being uploaded to the USDA site.
After the initial farm audit inspection occurs, an unannounced visit is possible within the remainder of the growing season. If the auditor left you with any areas that required corrective actions, it is important that you address and document actions so that you are ready for any follow-up visits.
Previous manuals and records must be retained for three years. It may be helpful to store previous records in separate binders and label them by the audit year.
Remember that your plan of action manual is what we call a “living document,” and should be updated as you make any changes during the growing season and from year to year. Be sure that any changes are appropriately documented. For any subsequent audit, always have the previous year’s audit manual on hand in case the inspector wants to see that any changes or corrective actions were documented.
GAP Certification Resources
Assessing On-Farm Produce Safety Risks Video Modules
Module 1, 8, and 9 of this series provides important information pertaining to GAP certification. The other modules (2-7) are helpful in performing a hazard analysis and identifying risks at each stage.
- Module 1: Accessing Virginia Market Sectors
- Module 2: Performing a Hazard Analysis
- Module 3: General Practices
- Module 4: Pre-Plant Stage
- Module 5: Production Stage
- Module 6: Harvest Stage
- Module 7: Post-Harvest Handling Stage
- Module 8: The GAP Audit Process
- Module 9: GAP Manual Preparation
USDA Agricultural Marketing Service Audit Verification Program
USDA AMS main page to their Good Agricultural Practices (GAP). Links to USDA GAP, HGAP, HGAP Plus, GroupGAP, and other audit schemes. Also lists certified farms by commodity and state, plus much more.
GAP Certification Programs: Removing Barriers to USDA GAP Programs website
Amber Vallotton collaborated with the NASDA Foundation to create a GAP Certification Programs overview, which includes the “Assessing Risks” factsheet series, along with helpful guidance, tips, and resources. This is an excellent tool to help guide you!
Bridging the GAPS Farm Guide: Good Agricultural Practices and On-Farm Food Safety for Small, Mid-Sized, and Diversified Fruit and Vegetable Farms
Though a bit dated, this is a really nice guide to creating a plan of action manual by the Washington State Department of Agriculture.
Good Agricultural Practices for Small Diversified Farms: Tips and Strategies to Reduce Risk and Pass an Audit
A guide written by NCSU and the Carolina Farm Stewardship Association, which provides many tips for working through the audit process.
Virginia Cooperative Extension Mentors Growers in GAP Certification Preparation Series
This series of six videos showcases Virginia farmers and their stories of working with Virginia Cooperative Extension to have their farms become Good Agricultural Practices (GAP) certified.
GAP Recertification FAQs
Click on the questions below to see answers.